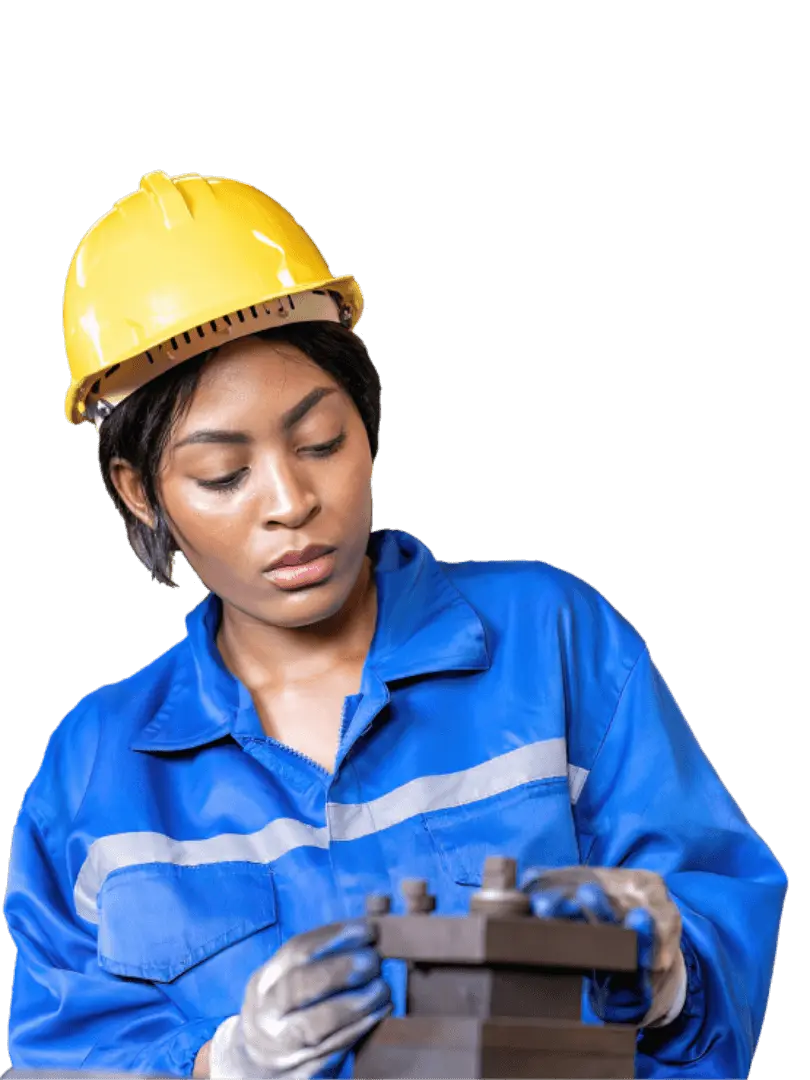
Lone Worker Safety Solutions for the Manufacturing Industry
The Shield: A Durable Lone Worker Device for Factory and Manufacturing Staff
This device is small enough to not get in the way but rugged enough to withstand the work of an active role. It’s trusted by manufacturers for supporting lone workers in high-risk environments, such as factory floors, warehouses, and processing plants.
Explore the safety features that manufacturing workers use to stay protected — from man-down alarms and GPS tracking to lone worker support during high-risk tasks or shift work.
Enhancing Lone Worker Safety in the Manufacturing Industry
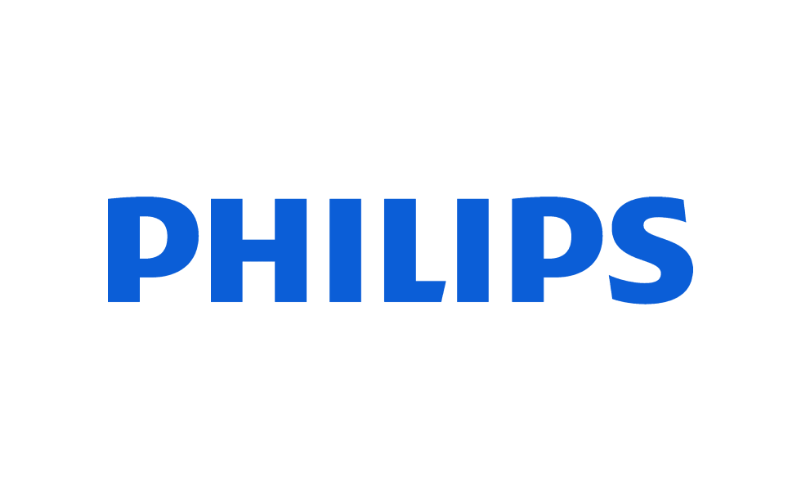
“SoloProtect definitely works. Our manager gets escalation calls when activated, ensuring immediate response and peace of mind for our team.”
Read the study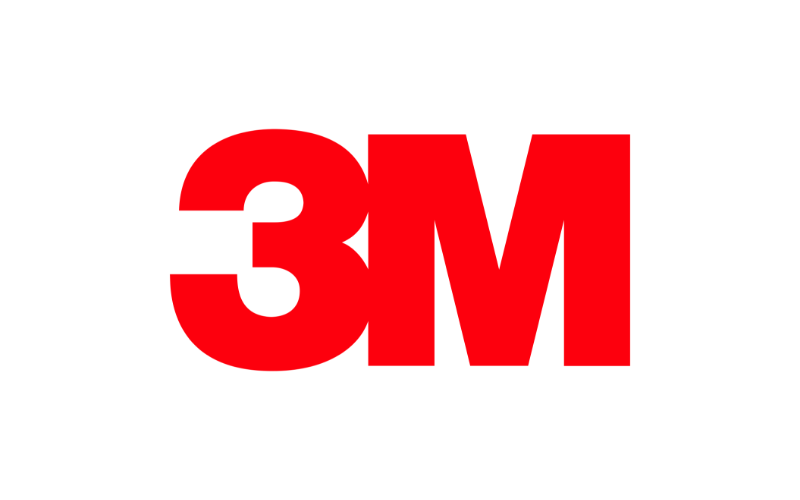
“The SoloProtect devices are exceptionally user-friendly and straightforward to manage, making them an ideal solution for our lone worker safety needs.”
Read the studyHow can manufacturing companies keep lone workers safe?
Manufacturing companies can enhance the safety of lone workers by equipping them with lone worker safety devices. These devices serve as personal safety alarms, allowing workers to quickly raise an alert in emergencies. When an alert is triggered, it connects to our Monitoring Centre where operators can assess the situation and dispatch the appropriate response, such as calling the police, an ambulance, or notifying a manager, colleague, or security team. These devices may also provide GPS tracking to locate workers rapidly during incidents.
What are the benefits of using SoloProtect’s lone worker safety devices?
SoloProtect’s lone worker safety devices offer several benefits, including an automatic alert in the event of a slip, trip, or fall, ensuring swift assistance reaches the worker. These devices enhance the safety and security of factory workers, warehouse staff, plant engineers, delivery drivers, and others who work in isolated or remote locations within the manufacturing industry. They provide peace of mind to both workers and employers, helping to reduce risks and improve overall worker safety.
Are there specific regulations that manufacturing companies must follow to protect workers?
Yes, there are a number of specific laws and regulations that apply to the manufacturing sectors, including but not limited to: The Health and Safety at Work Act 1974 (HASAWA), The Lifting Operations and Lifting Equipment Regulations 1998 (LOLER), The Dangerous Substances and Explosive Atmospheres Regulations 2002 (DSEAR) and Health and Safety (First Aid) Regulations 1981 to name a few. These regulations cover various aspects of workplace safety, and compliance with them is crucial to ensuring the wellbeing of manufacturing employees.
What types of manufacturing roles benefit most from lone worker safety devices?
Lone worker safety devices are ideal for a wide range of roles within the manufacturing sector, including machine operators, plant engineers, maintenance technicians, forklift drivers, and warehouse operatives. These employees often work in isolated areas, operate heavy machinery, or handle hazardous materials — all of which carry elevated risks. Equipping them with personal safety devices ensures they have immediate access to emergency support in case of slips, trips, falls, or unexpected incidents on the factory floor.